Sparks, smoke, crunch and burning smell: what can break in a drill or screwdriver

Diagnostics of a drill in a hurry
To find out exactly why your drill broke or what's wrong with the screwdriver, you need to give the tool to the service centre for diagnostics. But there are many direct and indirect signs by which it is possible to find out approximately in which node the problems occurred.
- If the drill does not turn on at all (and does not even hum), then almost one hundred percent of the problems lie in the electrical part. Moreover, the problem can be of any scale: from ridiculous (clogging of contacts on the button) to large (engine burnout or electronic control unit).
- If the power tool works somehow, intermittently, and desperately sparks, then the problem is most likely in the area of the anchor, collector or brushes. It is with the collector-brush assembly that most of the malfunctions are associated, because of which drills and screwdrivers do not work as well as expected from them.
- If strange sounds appeared during operation that did not exist before (squeaking, crunching, howling), or strange vibrations and beats appeared, then the problem is probably related to the mechanical part. For example, bearings can "squeal", gears can "crunch", and a shaft or cartridge can "knock".
- If the drill motor is humming and the chuck is not rotating, then the reason is probably a gearbox failure or a shaft jamming. A faulty gearbox and a jamming shaft can also cause the drill to turn the drill bit not as fast as we would like, and the screwdriver rotates the bit. not with the effort that is required.
- If the power of the drill has dropped for no apparent reason, then this may be due to increased losses: mechanical or electrical. In some cases, the cause of the power drop may be clogged bearings that do not rotate as freely as before. Sometimes the problem lies in the burnt armature windings, due to which the resistance in the circuit increases, and the engine becomes unable to develop its rated power.
- If the drill overheats, smokes or smells burnt, then the problem can be any: mechanical, electrical, clogging, wear or banal damage due to careless operation. Often, the reason also lies in the fact that someone decided to "set the heat" and subjected the tool to loads for which it is simply not designed.
So, we briefly figured out why a drill, a screwdriver or a rotary hammer can work badly. Next, we will look at the typical causes of malfunctions in more detail and divide them into several categories: from easily fixable problems to cases where repair is impractical.
![]() |
A small Makita screwdriver in disassembled form. |
Not breakdowns at all
Some problems with drills and screwdrivers cannot even be called malfunctions. Such annoying troubles include the wear of collector brushes. Graphite brushes are consumables (sometimes drills are sold immediately with a spare set). They are more or less standardized, often interchangeable (running sizes fit different brands of tools) and cost literally pennies. Many drills do not even need to open the case to replace the brushes. This can be done without disassembling the power tool, if the manufacturer has provided special windows covered with plugs for access inside. A powerful power tool, like punchers, is even equipped with indicators that suggest that it's time to replace the carbon brushes.
If there is no indicator, then the brushes themselves will let the gawkers know that they have worn out. The most striking (literally and figuratively) sign of wear are powerful sparks that are visible through the slots of the housing and ventilation holes. An indirect sign is the operation of the tool with interruptions and jerks. Sparking occurs due to the fact that the brushes are not fully pressed by the springs to the collector. Sparking is accompanied by the release of heat. In addition to smoke and the smell of burning, which accompany sparks, the danger lies in the fact that due to overheating, the collector plates can deform and solder off from the base of the collector. That is, without changing the brushes in time, you can easily "screw up" the engine anchor.
The process of replacing brushes on the example of a DeWalt screwdriver. |
The "visual effects" described above almost do not happen with drills and screwdrivers with brushless motors. They generally have many advantages over tools with traditional motors (although the price is considerable). If something is sparking slightly inside the brushless screwdriver under load, then it is the engine brake (and this is quite a normal phenomenon, not a malfunction).
Almost no breakage
There are also problems that only look scary, but can be easily eliminated on their own with a screwdriver, sandpaper and a couple of strong words to the tool manufacturer.
- If the drill just won't turn on, start by checking the wire. Usually the cable is frayed near the plug or (which happens more often) at the entrance to the handle. The power wire can be easily and quickly changed to any other with the same core cross-section. If the problem is not in the power cable, then it's time to open the case and check the internal wiring. It happens that the wires inside the drill come off or are soldered off if the manufacturer does not pay due attention to the quality control of its products.
- Difficulties with turning on a drill or screwdriver may be associated with clogging of buttons and contacts. All switches are subject to this: the start button, the speed control and the reverse slider. If they stick or move tightly, then it is worth opening the tool and thoroughly cleaning it from dust, blowing with compressed air. All contacts should be thoroughly wiped with alcohol and cleaned with a fine-grained skin. This is quite a troublesome job (because the contacts and button details are so small).
- Sometimes the drill chuck does not hold well, and the rigging is loose in it. It often happens that the toothed crown has worn out, and it is impossible to tighten the drill with a key normally. These problems are eliminated in one single way — by replacing the cartridge.
- If a new drill stinks at the first turn-on, like from the exhaust pipe of a car, then this is not always a sign of a serious problem. This happens if there is too much grease in the gearbox or bearings. Being displaced through the cracks and falling on the heated parts of the tool, the excess solidol burns and gives a characteristic smell. The problem is solved by disassembling the tool (with loss of warranty) and removing excess grease.
![]() |
Bosch cordless screwdriver disassembled. |
Serious trouble
Some malfunctions, unlike those described above, can cause a lot of trouble and cost a pretty penny.
Excessive heating of the drill bearings (which can sometimes be recognized by the smoke and smell of burnt plastic, as well as the tight rotation of the cartridge and a loud "squeak") indicates serious problems. A part heated red-hot can melt the plastic body of the tool. When melting, the plastic will lose its shape, and there will be a significant backlash in the details. If the bearing is not lubricated or replaced, then over time it will collapse from overheating, or the anchor will jam. And until it breaks into pieces, it will spoil your nerves with a loud howl and take away part of the engine power.
If the impact drill has stopped taking concrete and brick, it means that its impact mechanism has completely worn out. An electric drill is not designed like a hammer drill. Instead of a "drunk" bearing or a crank mechanism, it has two ratchets with wavy surfaces that slide over each other, providing light blows with a drill on concrete. Over time, these "waves" naturally wear out, ratchets turn into flat washers, and a drill or screwdriver that previously knew how to drill concrete turns into an ordinary non-impact tool. It is possible to restore operation in the drilling mode with impact only by repairing and replacing worn parts. Therefore, if you need to drill concrete not from time to time, but regularly, it is better to immediately buy a normal drill.
![]() |
Bosch three-mode punch in disassembled form. |
Almost hopeless cases
Serious breakdowns of engines and gearboxes are almost a "verdict". We use the word "almost" because a repair with a full restoration of the functions of the tool is still possible. But sometimes (especially in the case of a brushless power tool) the cost of repair is comparable to the price of a new device.
The reasons for engine failure may be:
- defective or initially poor quality — engines whose winding is wound from too thin or low-quality copper wire simply cannot withstand prolonged work or heavy loads and burn out, emitting a thick blue smoke;
- insulation failure and short circuit — the "reservation" of the electric motor (that is, the heat-resistant varnish with which the windings are abundantly covered) can be damaged as a result of exposure to abrasive particles (dust, metal particles, fine concrete chips) that fall inside the drill body during operation.
Drill gearboxes break down due to poor metal quality, loose gears, lack of lubrication, or (which happens much more often) due to excessive loads. If the slots on the shaft are "licked" or the teeth of the gear are broken off, then the entire assembly needs to be sorted out or changed entirely. It is better not to disassemble the planetary gearbox of a drill or screwdriver on its own (except in cases when only the lubrication is replaced), because there are a lot of small parts in it: gears, washers and seals.
![]() |
Kobalt brushless screwdriver disassembled. |
Let's summarize the results
There are many reasons why a power tool can spark, smoke, hum and vibrate when working. Many of them are associated with improper operation and excessive loads. Therefore, it is necessary to choose screwdrivers and drills correctly, based on specific tasks and working conditions. And if you just need a good tool, then you should pay attention to the products of Bosch, DeWalt, Makita, Metabo, AEG or another company with an excellent reputation. The listed manufacturers have service centers in almost every region of the country, and you can buy spare parts for drills and screwdrivers of these brands almost freely.
Articles, reviews, useful tips
All materials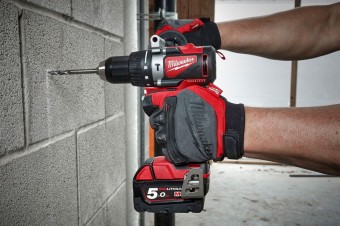
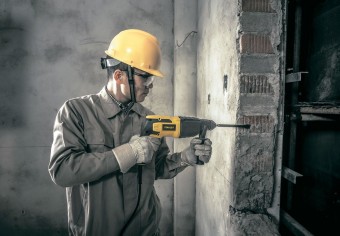
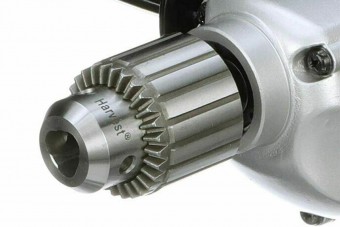

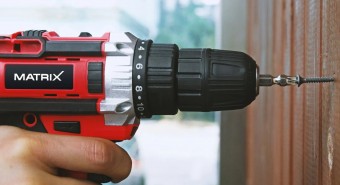
